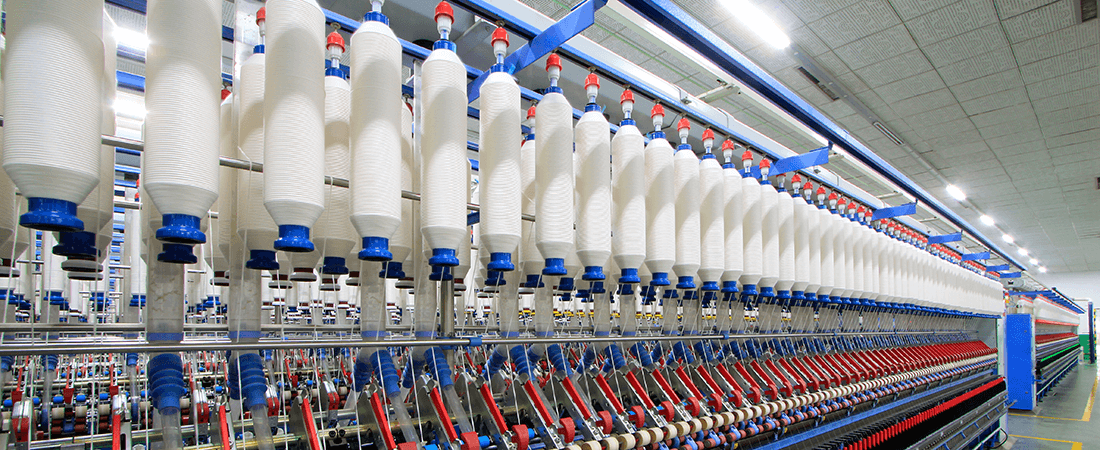
Energy saving by 13% achieved with inverter type unit + α!
Lower pressure and even more energy saving was achieved by a bit of ingenuity on installing inverter units.
-
Seeking to implement measures to save energy with compressor equipment
-
Seeking to reduce pressure of compressor equipment
Implementation of inverter type units with line pressure control and group control
- Discharge pressure reduced by 1.5 bar
- Electric power consumption reduced by about 160,000 kwh annually
VS55A4 x 1 unit, SG55A4 x 2 units and line control (optional)
1. Implementation of inverter type units with line pressure control and group control
Operation involved fixed speed type units only in the past. Since the required amount of compressed air varies significantly depending on the number of units operated by the facility, inverter type compressors that are expected to offer optimum energy savings according to respective operating status were selected.
Furthermore, line pressure control was implemented to inverter type units and pressures are detected at ends (before use-point) to implement capacity control.
There is no longer any need to secure any margin for pressure settings and optimized pressure settings near use points became possible at all times for operations, achieving a pressure reduction of about 1.5 bar in comparison with previous operations with conventional fixed speed type units
In addition, using group control functions, which are standard functions of compressors, makes it possible to operate fixed speed type units with the same pressure as inverter type units, achieving energy saving of about 13% for the system as whole (annually about 120,000 kwh).