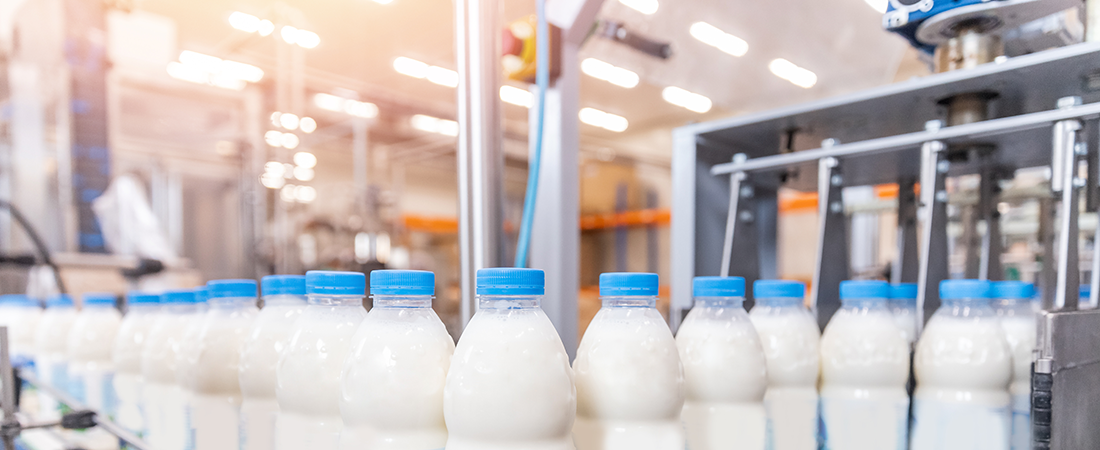
Heat of Compression(HOC) dryers was implemented to save energy! Central management of operating information was also made possible through central monitoring!
Energy saving by about 300,000 kwh per year was achieved by implementing inverter type units and Heat of Compression(HOC) dryers, based on analysis of actual operational data. Furthermore, the customer’s corporate internal network was also linked to facilitate a centralized monitoring of operating status.
- Seeking to implement measures to save energy with compressor equipment
- Seeking to centrally monitor operating statuses of compressors, by utilizing a corporate internal communication network.
Inverter type units and Heat of Compression(HOC) dryers were implemented and operational data is centrally monitored through a group controller.
- Electric power consumption reduced by about 300,000 kwh annually
- Central monitoring achieved through coordination of air compressor Modbus and plant internal communication network system
ALE160WV x 3 units, ED160W x 3 units and group controller
1. Implementation of inverter type units and a group controller
Since a difference between peak and non-peak loads was found as a result of measuring facility load status over a one week period, inverter type compressors that are expected to offer optimum energy savings were selected.
The unloaded operating time of units increased when the operating load of the plant was lower, creating loss of energy. Consequently, in order to automatically stop operation of unnecessary equipment to minimize unloaded standby time, a group control system was implemented.
2. Implementation of Heat of Compression(HOC) dryers
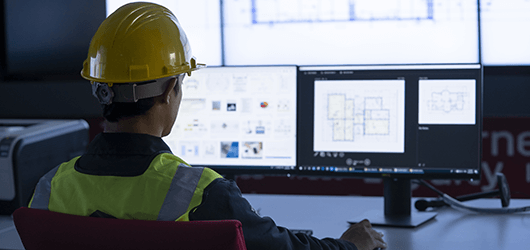
3. Central monitoring
Modbus is mounted on the compressor to communicate with a group controller, while analog signals from flow meters are input to the group controller. Operation data and flow data of respective units are displayed all together on a group controller, while a consolidated monitoring from a center is possible, by coordinating the plant internal communication network via the group controller PLC.
It became possible to gain information about compressor operation status at all times, making it possible to initiate responsive actions rapidly, in an event an unexpected alarm is triggered.