








Setting a new standard for specific energy performance in its class. The future of mid-range Oil-free.
By optimizing energy efficiency throughout the entire system, we have set a new benchmark for specific energy performance in its class. A mid-range model that paves the way for the future with cutting-edge performance.
Best energy efficiency in mid-range models.
Class-leading specific power consumption
With specific power consumption as our primary design criterion, we strive to deliver products that maximize energy efficiency for our customers. The integration of ultra-high-efficiency motors and optimized package design has enabled us to set a new benchmark for specific energy performance in its class.

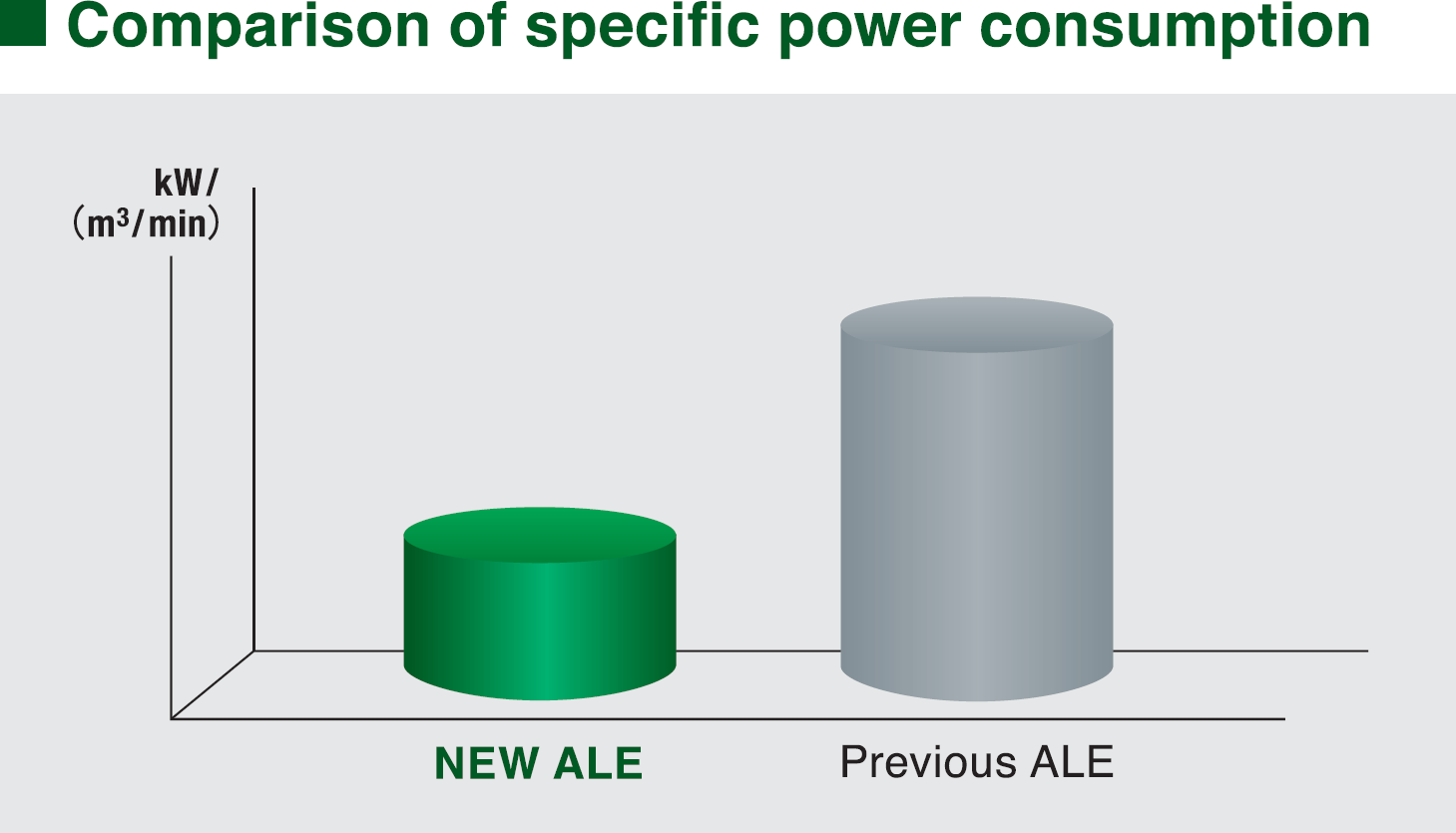
Wide-range control
Wide range control can deliver higher airflow at lower pressure point. ALE IV senses line pressure and automatically utilizing excess power during low-pressure operation efficiently. At 0.6MPa operation, airflow can be increased by up to 10% (75kW).

High-efficient motor (Fixed-speed: IE4, Inverter: IE5 equivalent)
To pursue energy efficiency, we adopt high-efficiency motors. ALE IV fixed-speed models are equipped with IE4 super-premium motors, and inverter models feature ultra-high-efficiency IPM motors which are IE5 equivalent.

Designed high effiiency screw rotors
A new rotor profile has been designed using advanced analysis technology that KOBELCO has fostered in their long history since developing the first oil free screw compressor in Japan in 1956. KOBELCO has achieved class-leading specific energy consumption thanks to the screw rotors which have been designed superior performance.

●Optimization of the inter stage pressure
●Optimization of rotor clearance
●Improvement of shaft sealing structure
Package design for no wasted energy
Internal piping design, high efficiency motors and fans contribute to energy savings. Moreover, gas coolers' optimization decreases the discharge temperature and downsizes auxiliary equipment such as dryers. This leads energy saving of not only compressors but also clean air systems.

Partial-load performance of Inverter model
Inverter model's partial load performance has been improved thanks to IPM motor and superior rotor design. Inverter model supplies required air volume in appropriate power consumption.
Stable pressure control of Inverter model & Energy saving logic of Fixed speed model
Stable pressure control of Inverter model keeps the line pressure lower. And the pressure fluctuation is kept within 0.01MPa. Energy saving logic of Fixed speed model forcibly switch loading to unloading at every capacity control cycle (min 23sec). Excessive pressure rise is eliminated and energy loss is minimized.
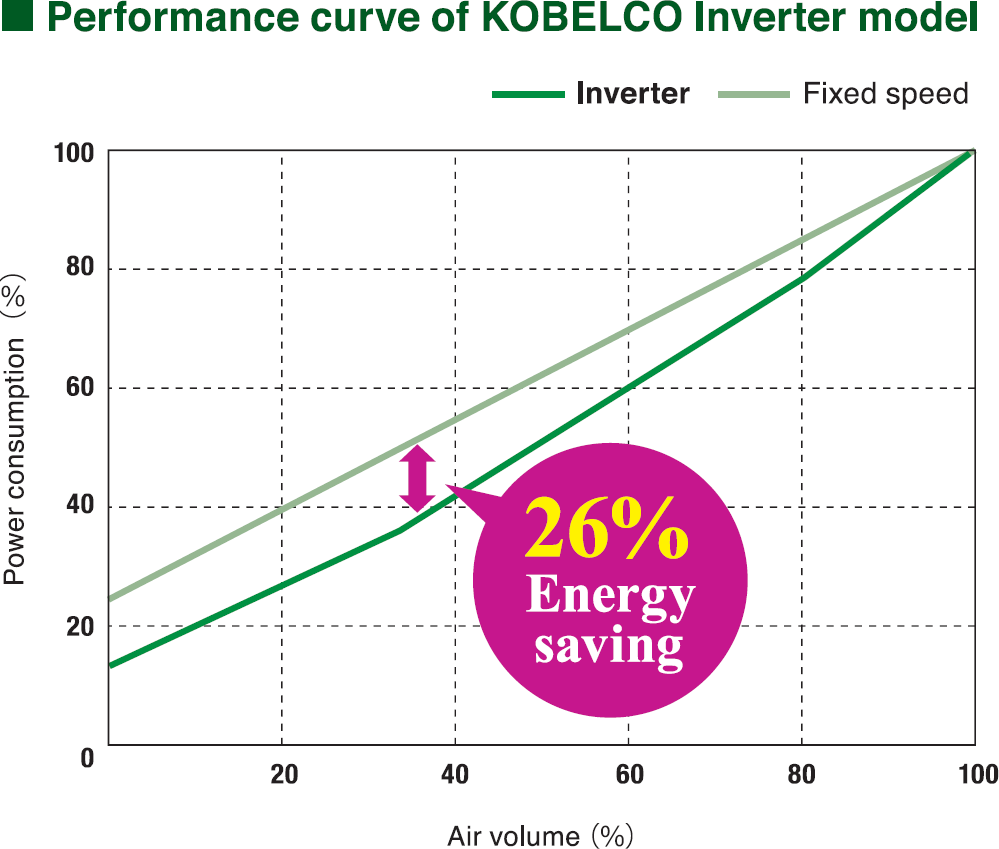
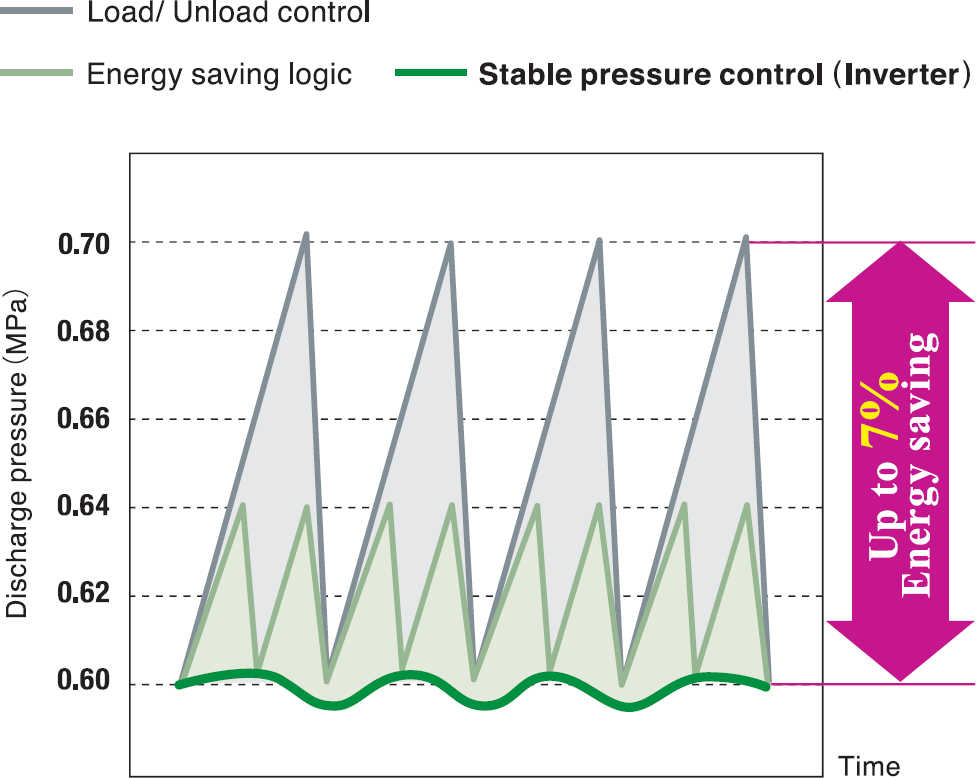
Class 0 certified
KOBELCO has received Class O certification (ISO8573-1 [:0]) for (Emeraude ALE) series from international test institute called TÜV which certifies the highest level of purity for quality classifications of compressed air.
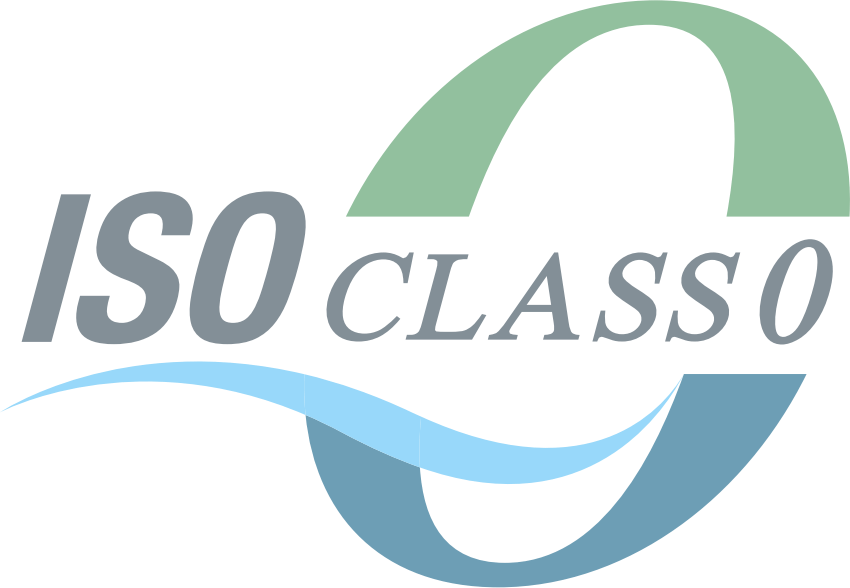
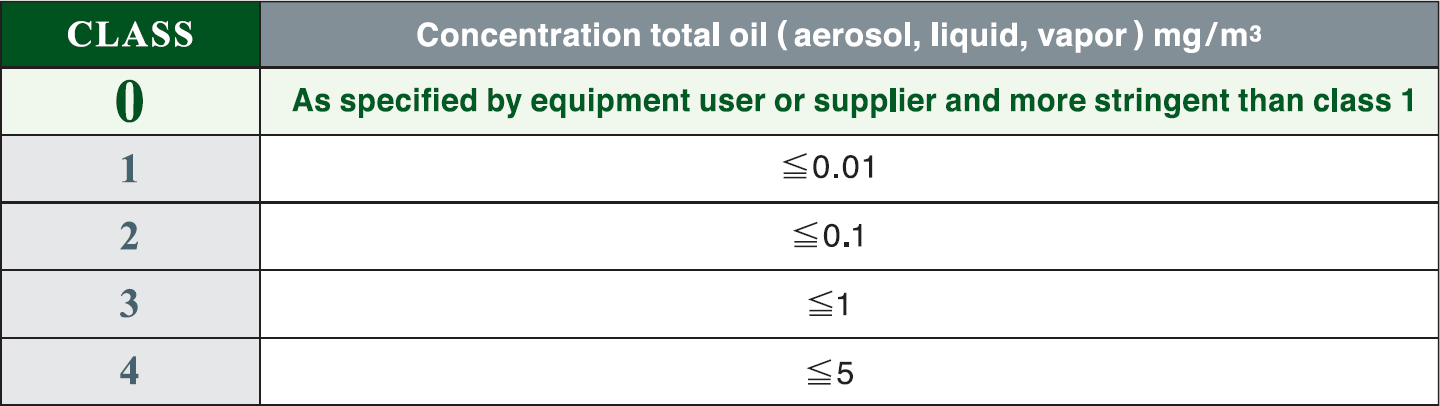
Long life cycle
Long Overhaul cycle has been achieved thanks to long life cycle bearings.

Superior Anti-corrosion performance
Proven Teflon coating and 2nd stage's Stainless steel rotors secure high durability against drain attack and prevent performance deterioration due to corrosion.
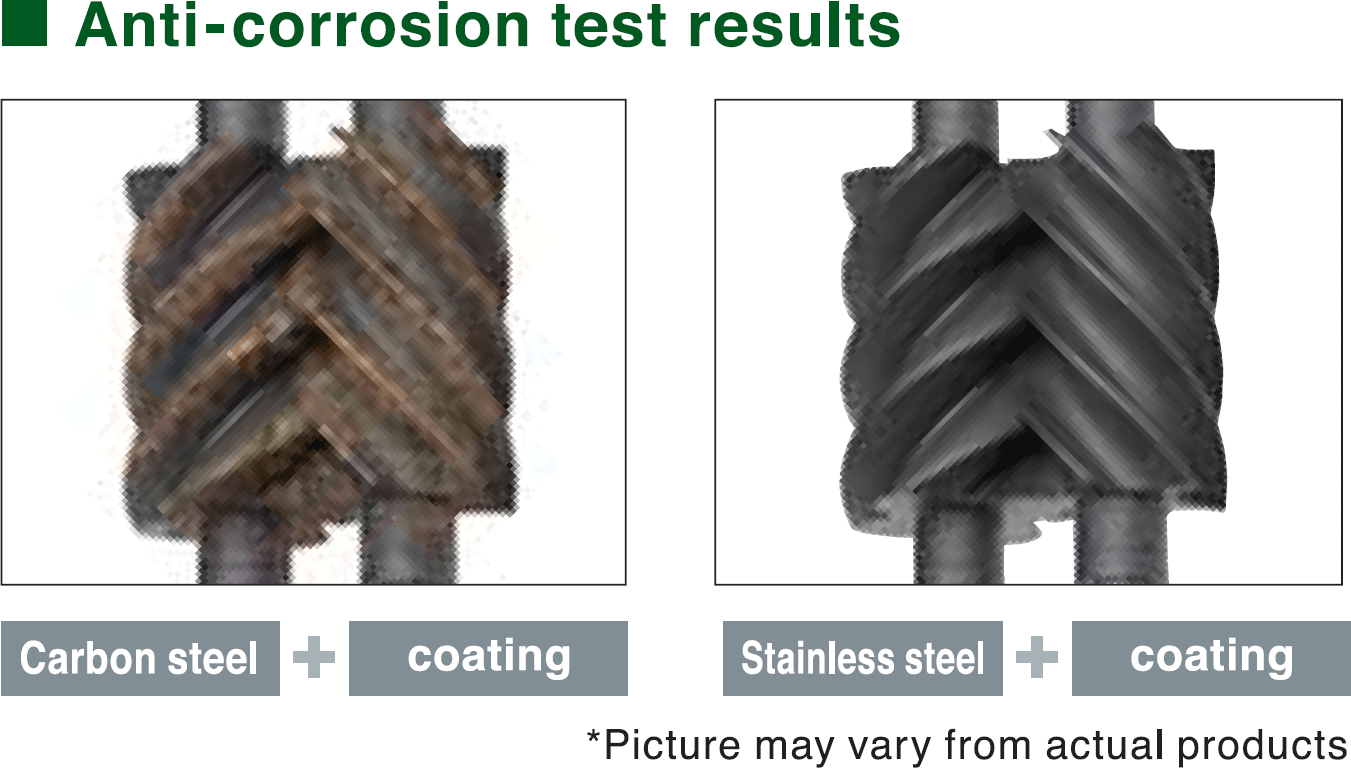
Outstanding quietness
Various noise control techniques has drastically reduced sound level. Making the working environment more comfortable.
Package structure for noise reduction
Cooling air inlet points have been put into one place to reduce noise.
Panel design
Noise absorbing material and high sealing ability against abrasive noise reduce noise leakage.
Silencer
Newly designed suction and discharge silencers reduce noise level.
Easy maintenance
Easy access to key service parts for maintenance thanks to large panels and reduction of internal piping.
Exhaust cleaner without power source or instrument air
Filter type and compact exhaust cleaner has over 99% of oil mist separation performance and keeps inside of unit clean. Moreover, pressure resistance doesn't increase for long time because oil mist is separated itself.
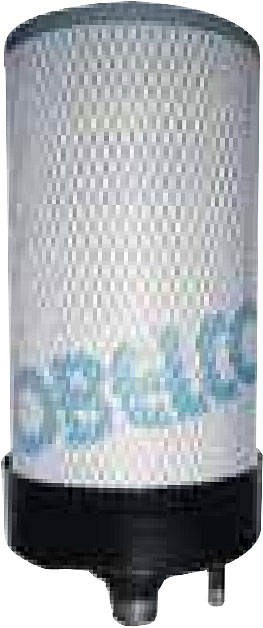
Enhancing usability with touchscreen controller
Equipped with a 7-inch full-color touch screen controller, it allows for easy monitoring of compressor operation and various settings.
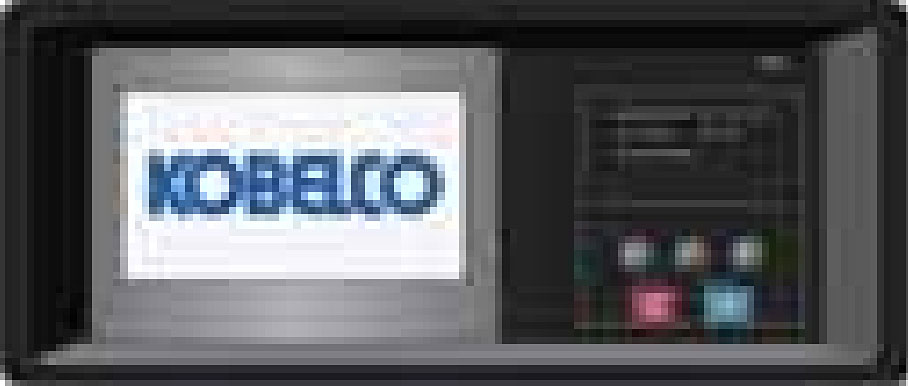
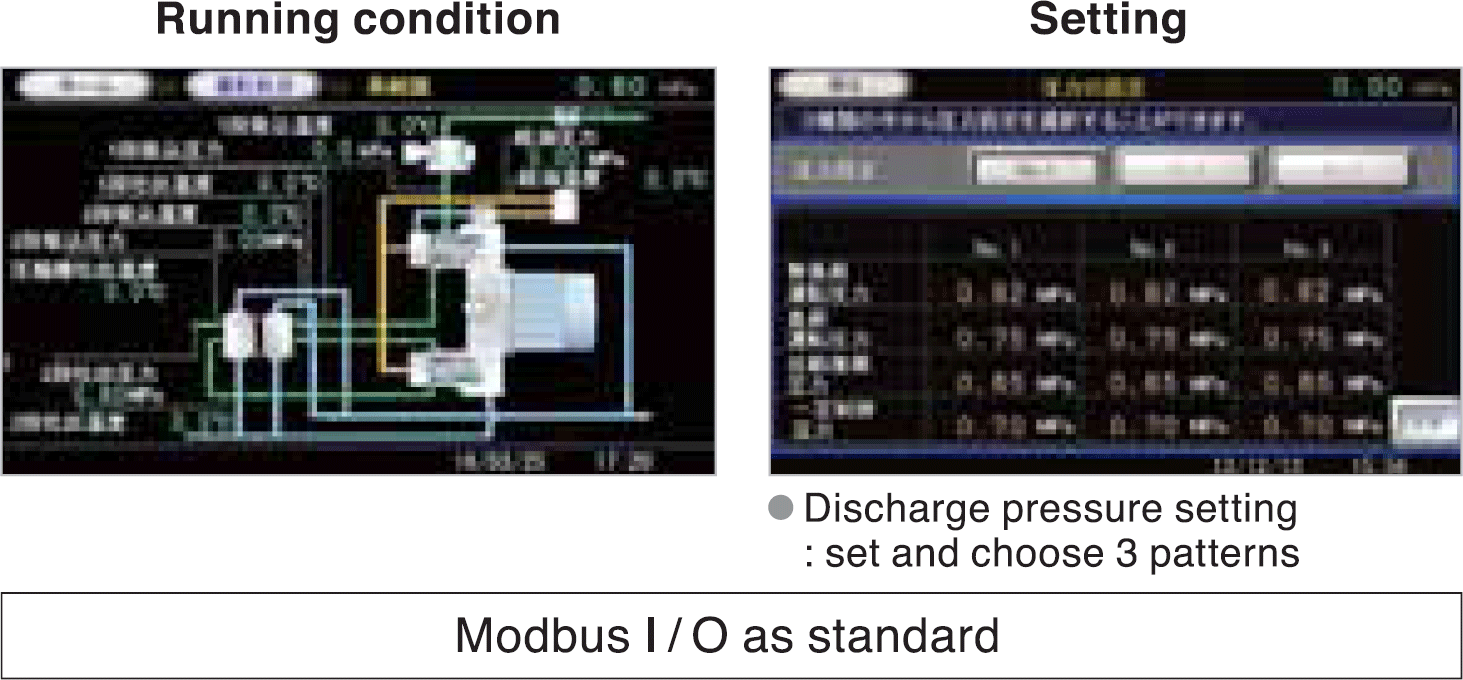
Group control (up to 6 units)
By interconnecting multiple units, max, 6 units can be automatically operated, achieving optimal energy-saving operation without group controller.
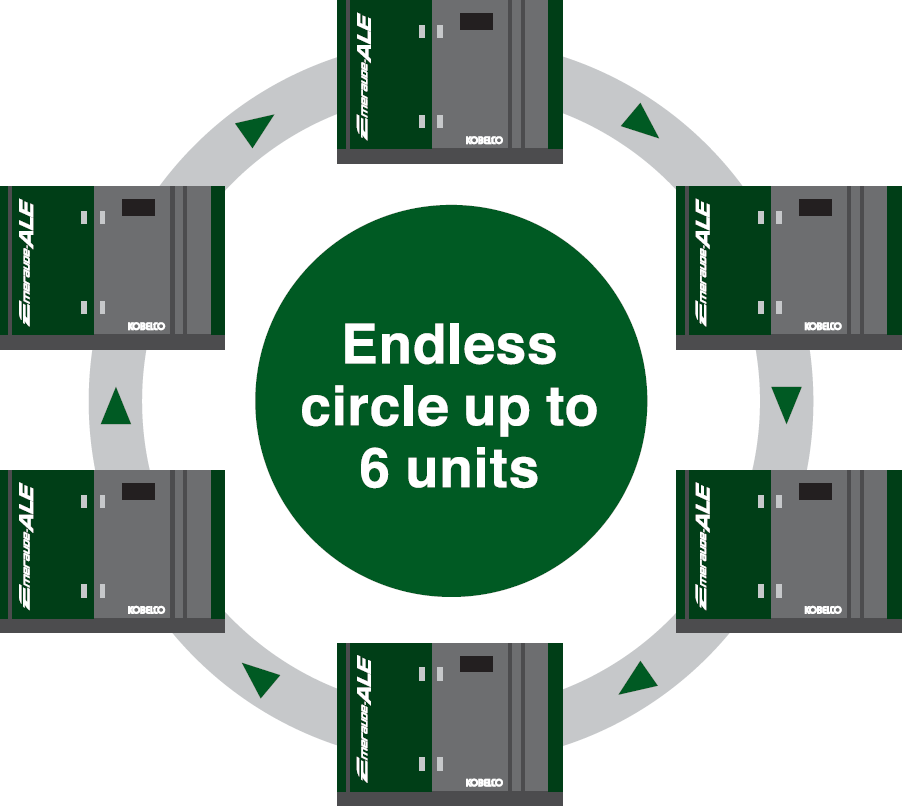
Protection features
●7500V surge protector
●Water flow switch (for water cooled model)
●Emergency stop button
●Motor winding temperature detection
●Password protection
●Power failure protection (within 0.5sec)
●Auto restart after power restoration (within 20sec)
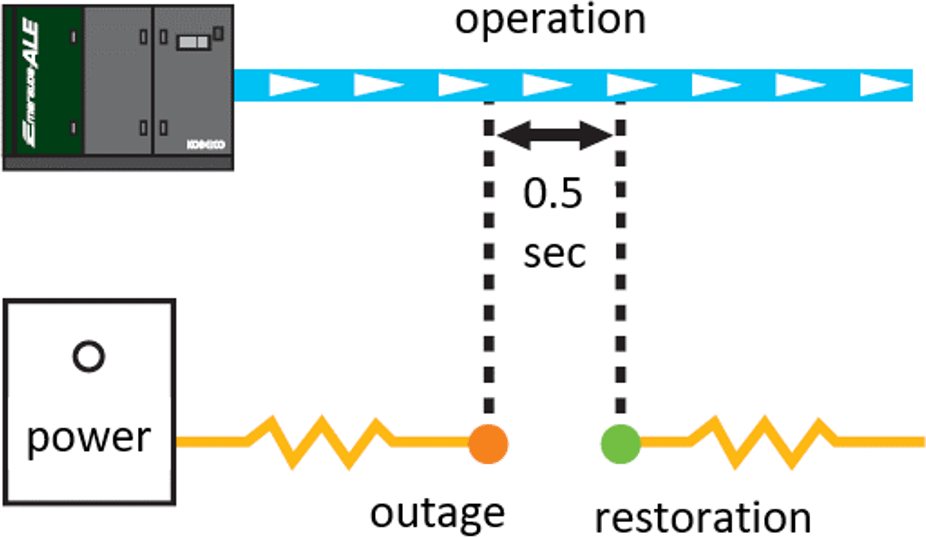
Inverter / Water cooled model

Inverter / Air cooled model

Motor specifications: IPM motor, 6-pole totally enclosed fan-cooled, Insulation class F, Rated for continuous use, Drive system: Step-up gear.
Fixed speed / Water cooled model

Fixed speed / Air cooled model
