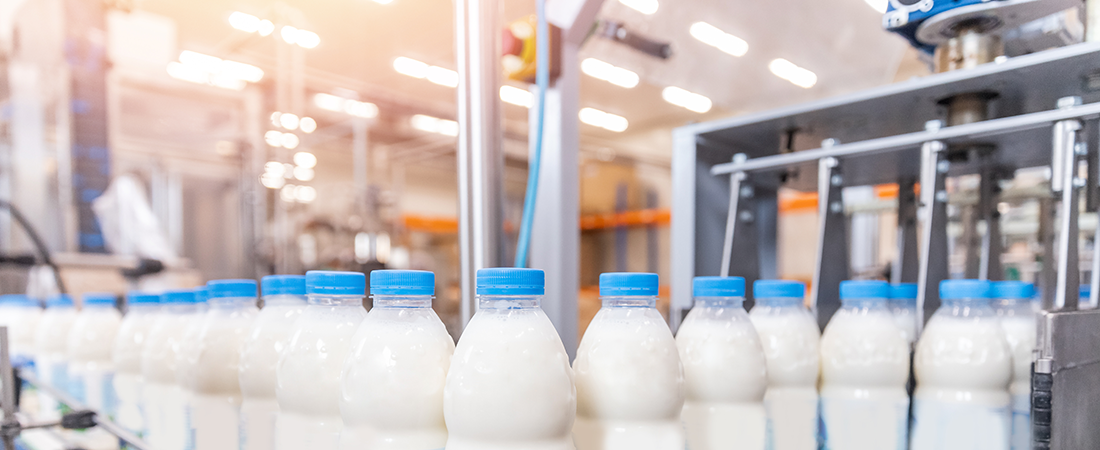
เครื่องทำลมแห้งแบบใช้ความร้อนอัด (HOC) ได้รับการใช้งานเพื่อเป็นการประหยัดพลังงาน! การจัดการข้อมูลกลางในส่วนการดำเนินงานสามารถดำเนินการผ่านระบบการตรวจติดตามจากส่วนกลาง!
ประหยัดการใช้พลังงานได้ประมาณ 300,000 กิโลวัตต์-ชั่วโมงต่อปี โดยการใช้ยูนิตประเภทอินเวอร์เตอร์และ เครื่องทำลมแห้งแบบใช้ความร้อนอัด (HOC) อ้างอิงจากการวิเคราะห์ข้อมูลการดำเนินงานจริง นอกจากนี้ เครือข่ายต่าง ๆ ภายในองค์กรของลูกค้ายังได้รับการประสานเชื่อมโยง เพื่ออำนวยความสะดวกต่อการตรวจติดตาม สถานะการดำเนินงานจากส่วนกลาง
- มองหามาตรการประหยัดการใช้พลังงานผ่านอุปกรณ์คอมเพรสเซอร์
- มองหาวิธีการตรวจติดตามสถานะการดำเนินงานต่าง ๆ ของคอมเพรสเซอร์จากส่วนกลาง ผ่านเครือข่ายเพื่อการสื่อสาร ภายในองค์กร
เมื่อใช้งานยูนิตประเภทอินเวอร์เตอร์และเครื่องทำลมแห้งแบบใช้ความร้อนอัด (HOC) ข้อมูลการดำเนินงานจะได้รับ การตรวจติดตามจากส่วนกลาง ผ่านระบบควบคุมแบบกลุ่ม
- ปริมาณการใช้พลังงานไฟฟ้าลดลงประมาณ 300,000 กิโลวัตต์-ชั่วโมงต่อปี
- การตรวจติดตามจากส่วนกลางสามารถกระทำผ่านการดำเนินงานร่วมกันระหว่างเครื่องอัดอากาศ Modbus และระบบ เครือข่ายเพื่อการสื่อสารภายในโรงงาน
ALE160WV x 3 ยูนิต, ED160W x 3 ยูนิต และระบบควบคุมแบบกลุ่ม
1. การใช้งานยูนิตประเภทอินเวอร์เตอร์และระบบควบคุมแบบกลุ่ม
เนื่องจากพบความแตกต่างระหว่างปริมาณการใช้พลังงานไฟฟ้าสูงสุดและปริมาณการใช้ พลังงานไฟฟ้าที่ไม่ถึงระดับสูงสุด จากการตรวจวัดสถานะปริมาณการใช้พลังงานไฟฟ้า ณ สถานที่นั้นในระยะเวลาหนึ่ง สัปดาห์ จึงมีการเลือกคอมเพรสเซอร์ประเภทอินเวอร์เตอร์ต่าง ๆ ที่คาดว่าจะช่วยประหยัดการใช้พลังงานได้อย่าง เหมาะสม
ระยะเวลาการทำงานแบบสภาวะอันโหลดของเครื่องเพิ่มขึ้น เมื่อการทำงานแบบสภาวะโหลดของโรงงานลดลง ซึ่งเป็นเหตุ ให้เกิดการสูญเสียพลังงาน ดังนั้น ในการระงับการทำงานของอุปกรณ์ที่ไม่จำเป็นโดยอัตโนมัติเพื่อลดเวลาสแตนด์บาย แม้ไม่ได้ใช้งาน จึงมีการใช้งานระบบควบคุมแบบกลุ่มต่อไป
2. การใช้งานเครื่องทำลมแห้งแบบใช้ความร้อนอัด (HOC)
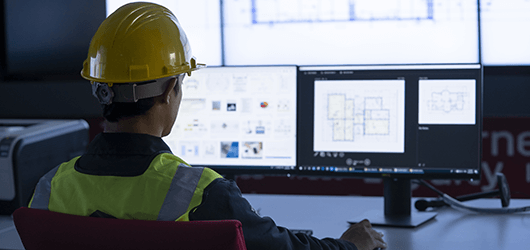
3. การตรวจติดตามจากส่วนกลาง
โปรโตคอล Modbus ได้รับการติดตั้งบนคอมเพรสเซอร์เพื่อสื่อสารกับระบบควบคุมแบบกลุ่ม ส่วนสัญญาณแอนะล็อก จากเครื่องตรวจวัดการไหลเวียนจะถูกป้อนเข้าสู่ระบบควบคุมแบบกลุ่มเช่นกัน นั่นคือ ข้อมูลการดำเนินงานและข้อมูล การไหลเวียนของยูนิตต่าง ๆ ที่เกี่ยวข้องทั้งหมดจะแสดงพร้อมกันบนระบบควบคุมแบบกลุ่ม การรวมระบบการตรวจ ติดตามจากส่วนกลางจึงสามารถทำได้ผ่านการประสานเครือข่ายเพื่อการสื่อสารภายในโรงงาน ด้วยระบบควบคุมแบบ กลุ่ม PLC
ทั้งนี้ การได้รับข้อมูลเกี่ยวกับสถานะการทำงานของคอมเพรสเซอร์ในทุกช่วงเวลาจึงสามารถทำได้ ส่งผลให้เริ่มต้น การตอบสนองได้อย่างรวดเร็ว ในกรณีที่พบการแจ้งเตือนอันเนื่องมาจากเหตุไม่คาดคิด